先进航空发动机的高性能要求设计大量采用整体结构、轻量化结构、先进冷却结构以及复合材料、粉末冶金、金属间化合物等新型材料,而这些零组件需要依靠特种加工成形。本文研究了电火花、电解、激光、超声和水射流等特种加工技术的特点及其在先进发动机中的新应用,说明了特种加工技术的优势以及在先进发动机研制中突显的特殊作用。
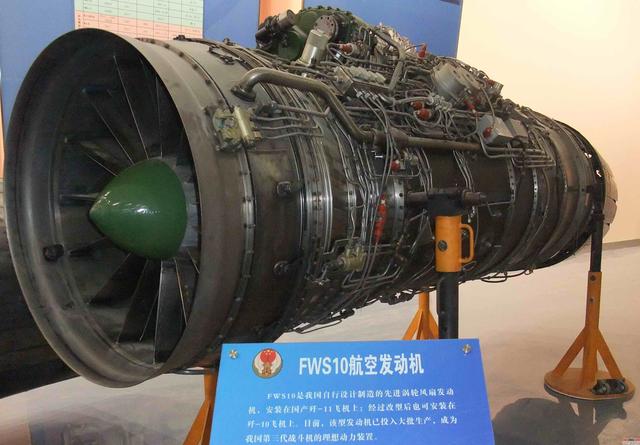
1. 航空发动机材料和技术特点
航空发动机在高温、高压且高转速的极端恶劣条件下工作,同时要求重量轻、油耗低、可靠性高、寿命长、能重复使用,是多学科交融的高端产品。其特征是核心技术的堆集,没有核心技术就没有现代先进发动机。现代先进航空发动机对单位推力、推重比、超声速巡航、推力矢量功能、隐身性能、高可靠性、长寿命和良好的维修性等性能要求更高,对材料和制造技术的要求更苛刻,由此带来:从普通合金到新型耐高温、轻质高强合金的应用;从金属材料到大量非金属材料、复合材料的应用;从机械加工到特种加工的转变;从减材制造到精密成形和增材制造;从保证几何形态为主到表面完整性控制为主;从试验验证为主到仿真验证为主;从单工序研究到多工序耦合规律研究;从数字化、自动化、信息化到智能化制造等。
先进发动机新材料和复杂结构使零件加工变得越加困难,有些甚至传统机械加工根本无法实现,而特种加工技术在某些领域成为不可替代的技术,并且应用越来越广泛,弥补了传统机械加工的不足。目前,传统的电火花加工、电化学加工、激光加工、电子束及离子束加工等特种加工技术已在航空发动机制造中大量应用,但随着先进发动机新材料、新结构的出现,特种加工技术也得到了新的发展和应用。闭式整体叶盘的多轴电火花加工技术、整体叶盘的精密电解加工技术、陶瓷基复合材料的超快激光加工技术、激光冲击强化技术和高压水射流强化技术等,对先进发动机新材料、新结构零件研制,以及提高表面完整性、可靠性要求等方面都发挥了越来越重要的作用。
2. 特种加工技术在先进发动机上的应用
(1)电火花加工技术是应用最广泛的特种加工技术,在航空发动机制造上应用非常普遍,如电火花线切割加工、电火花成形加工、电火花磨削、电火花钻孔及电火花表面强化等。
近年来,随着先进发动机性能的提高,传统电火花加工技术的应用受到了一定限制,如新型发动机涡轮叶片采用单晶叶片,而电火花钻孔技术因其存在重熔层、微裂纹及热影响区等缺陷,而被禁止用于单晶叶片气膜孔加工。图1所示为涡轮叶片气膜孔电火花加工金相照片,重熔层厚度一般在0.01~0.04mm。
但与此同时,先进发动机整体叶盘等新结构零件的出现,又促进了电火花加工技术的发展和应用,如整体叶盘结构因其加工成本高、周期长,而发展了数控高效放电铣技术,又如带冠闭式整体叶盘受其结构影响机械铣削加工难以实现,而开发五轴联动电火花成形加工技术来解决这一难题,其工艺方法是五轴联动电火花成形加工,再辅以磨粒流加工来去除其加工表面的重熔层,从而满足了使用要求。图2所示是采用五轴电火花成形机加工的带冠整体叶盘的电极和试验件,图3所示为磨粒流加工的带冠整体叶盘。
(2)电解加工因其在特殊加工对象(如难加工材料或形状复杂、尺寸微小、刚度极低的零件)的加工中所具有的优势,尤其在航空发动机叶片、机匣等复杂型面零件制造领域得到广泛的应用,大幅提高了生产效率,降低了制造成本。
先进航空发动机因其性能设计要求, 压气机叶片材料一般选用先进的镍基高温合金或钛合金以及钛铝合金等新型材料,并且采用弯掠等三维设计的特殊叶形,加工难度大、易受切削力影响而变形,精度要求高。传统的机械加工和电解加工都难以满足这种高精度复杂叶型的加工要求。精密电解加工技术(PECM)就是为适应这种特殊的加工要求而产生,在薄型面、小半径的叶片叶形加工上发挥了其独有的优势, 加工精度达到0.03mm,满足了先进航空发动机的需求。
精密电解加工也是整体叶盘诸多制造方法中的优选方法之一,它可以实现从整体叶盘毛坯到最终叶片型面成形的完整工艺过程。一般采用初成形和终成形两步,初成形采用套料加工方式去除大部分材料,终成形采用仿形加工方式,最终可达叶片型面轮廓精度≤0.06mm,高温合金材料表面粗糙度值Ra≤0.2μm,实现整体叶盘无余量精密制造,从而代替了数控铣削和人工抛光,可提高生产效率数倍,降低制造成本50%以上。
( 3 ) 电液束加工孔深径比达150/1 , 孔直径范围为0.13 ~ 1.5 m m, 孔加工精度±0.025mm,表面粗糙度值为Ra=1.6μm,孔出入口自然形成小R 圆角、无锐边。电液束加工的小孔如图4所示。
电液束加工涡轮叶片气膜孔表面完整性好,无重熔层、微裂纹及热影响区,加工单晶合金没有再结晶的风险,因此已成为先进发动机单晶叶片气膜冷却孔加工的首选工艺。
(4)激光加工技术最早应用在发动机燃烧室、加力筒体外部壳体的切割和涡轮叶片制孔等方面,但因传统激光加工受加工精度、重复精度低的限制,所以在发动机的应用不多。但对一些特殊零件,采用激光打孔,可取得较好的效益,如采用YAG激光旋切加工,用于涡喷发动机涡轮叶片气膜孔加工,后逐步被电火花高速钻孔取代。另外对高硬度、非导体材料的微小孔及数量很大的群孔零件加工,也很有优势,如发动机扩散器隔热屏、火焰筒内外壁等结构件打孔加工,目前在发动机上应用较广。
随着激光技术的发展,激光焊接、激光增材制造、激光冲击强化、水导激光加工及激光清洗等新技术不断开发并应用,为先进发动机制造提供了更多的技术选择。如激光冲击强化技术,具有金属表面强化层深、表面残余压应力、可达性好且效率高等优点,显著提高材料的抗疲劳、磨损和应力腐蚀等性能,产生的残余压应力深度可达1~2mm,是超声喷丸的3~5倍,常规喷丸的5~10倍,具有提高抗疲劳强度、延长疲劳寿命、抑制裂纹的形成与扩展等优势,因而成为先进航空发动机整体叶盘、叶环叶片表面强化的关键技术。
(5)高压水射流加工技术在发动机零件切割、钻孔及清洗等方面已广泛应用。此外,在新型复合材料的切割加工以及整体叶盘特殊结构零件的加工等方面也开展了探索性研究,并发展了用于去除发动机叶片涂层的水剥离技术。
水射流强化技术是利用高压水射流冲击工件产生的冲击力,来实现对金属材料表面进行强化的。在提高材料疲劳性能的基础上,可以获得良好的材料表面质量。在先进发动机涡轮盘等零件上已经明确提出了水射流强化需求。
3. 特种加工技术展望
特种加工技术在先进航空发动机制造中发挥了不可替代的作用,可以说“没有特种加工就无法制造出先进的发动机”。此外,还有电解磨削、磨粒流、离子束和电子束等特种加工新技术,在国内外的一些大学、研究所和企业被不断开发和应用。随着先进发动机新材料、新结构的不断涌现,原有特种加工技术也拓展了新的用途,如镍铝基新材料叶片的可切削性非常差,而电解加工非常适合加工且能够满足精度要求,又如新型多孔层板结构就采用传统的照相电解加工方法,而超快激光冷加工技术的出现则为单晶叶片气膜孔加工带来新的解决方案。
特种加工技术已经广泛应用于先进发动机机匣、整体叶盘、单晶叶片及复合材料等各种难加工材料和特殊结构零件研制中,解决了研制难题。而先进发动机技术的快速发展,对制造技术的要求永无止境,对特种加工制造技术的发展提出了更高的要求,特种加工技术也正在向精密化、自动化和智能化的方向发展。
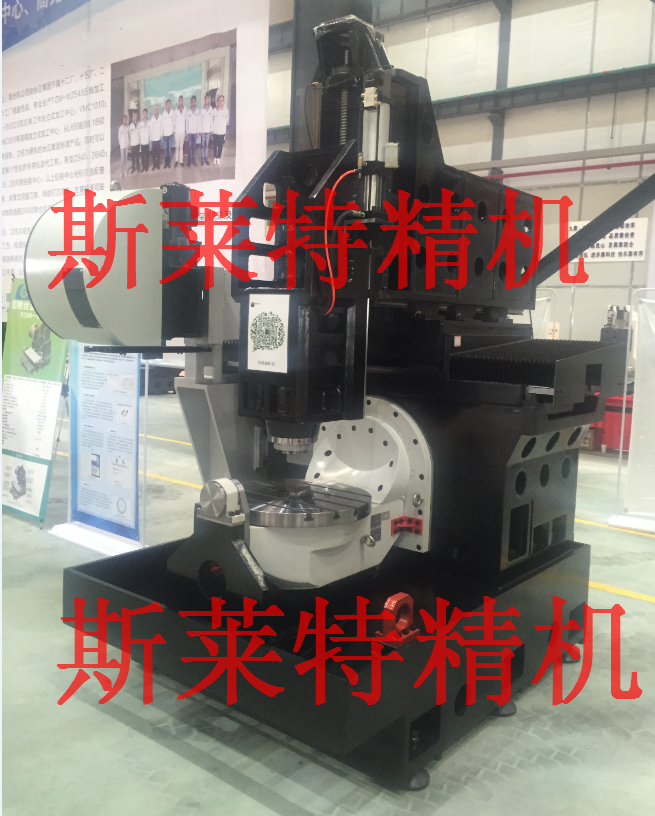
|